全員を器用に変える実験を開催した件
我々は中国など海外にながれた仕事を日本に取り戻そう。
というスローガンをうちたてました。
しかしコストが厳しい海外品をそのまま取り込んだら、
社員が疲弊するだけでだれも幸せになりません。
そのため、自動化、IT化、IOT化を進めているという話をしました。
そして、さらに我々働くメンバー全員がいかに効率よく生産性を挙げれるのか。というテーマで実験を行いました。
本日13時より、全員を器用に変えることができるのか?という実験を行いました。
管理しない管理とは?
今、トマト工業では、管理しない管理という大きなテーマをかかげ、動いています。
これ、どういうことかと申しますと、たとえば標準作業表を秒単位で製作して、そのように作業者が動いてるかどうかを
管理監督者が厳格にみきわめきっちりと管理する。
1秒単位でできているか確認し厳しく指導する。
ガチガチに管理する会社。
こんな会社があったとします。
たしかに経営層からすると非常に安心でき、そして管理は楽になると思います。
ちょっとイメージしずらいので、国に例えるとわかりますよね。
管理型と言えば、北の将軍様、あっ間違えた。
【北の黒電話様】
一方、自由形といえば、アメリカでしょうか。
どちらが現場からの自由な発想がでてくるでしょうか。
独裁者が管理型を選ぶのは、その方がやりやすいからです。
しかしガチガチの管理型だと【自由な発想】や、【改善提案】がでることはなくなってしまうと思います。
経営理念である【笑顔をつくる工場にしよう。】ここからズレる可能性が高いということです。
では、なにも管理しなくてよいのでしょうか?
実はそれが一番危なそうです。
管理なくそのまま個々人の生産性まかせでは、低い生産性で
高い生産性をもつ会社に簡単に負けて、市場から退場させられることになってしまいます。
自由な気質と、高い生産性。
この相反する2つの問題をどうやって取り組もうか?と悩みに悩んでいたところ、
効率的に動く【原理原則】を各自がインストールすることで、それを各自が現場現場で考えれば良いのではないか?
と思いつきました。
そうすれば、社員からすると、管理者に監視されることはありませんし、
現場からは自由な発想で、改善案がどんどんでてくる。
細かく管理しなくとも自動的に会社がうまくまわる。
これが理想論なのです。
これがみんなが幸せになる方法ではないかと思ったんです。
この考え方は実は、大野耐一さん著書のトヨタ生産方式からヒントを得ました。
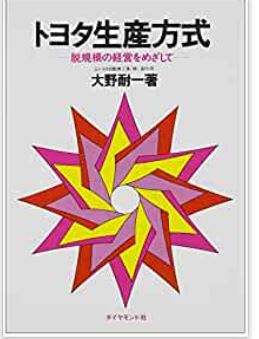
表紙だけみると、ゼロ秒で
”あーーー私むり、この手の本無理。ムリムリムリムリムリムリムリムリ。”
もうジョジョくらい無理を連呼してしまいますが、
私はこの本は、明日から小学校の教科書にすべきではないかとそう思っています。
いやむしろ、保育園の最初に見せる本はこれでいいんじゃないか。とすら思っています。
トヨタは大量生産しているように思われますが、実は違います。
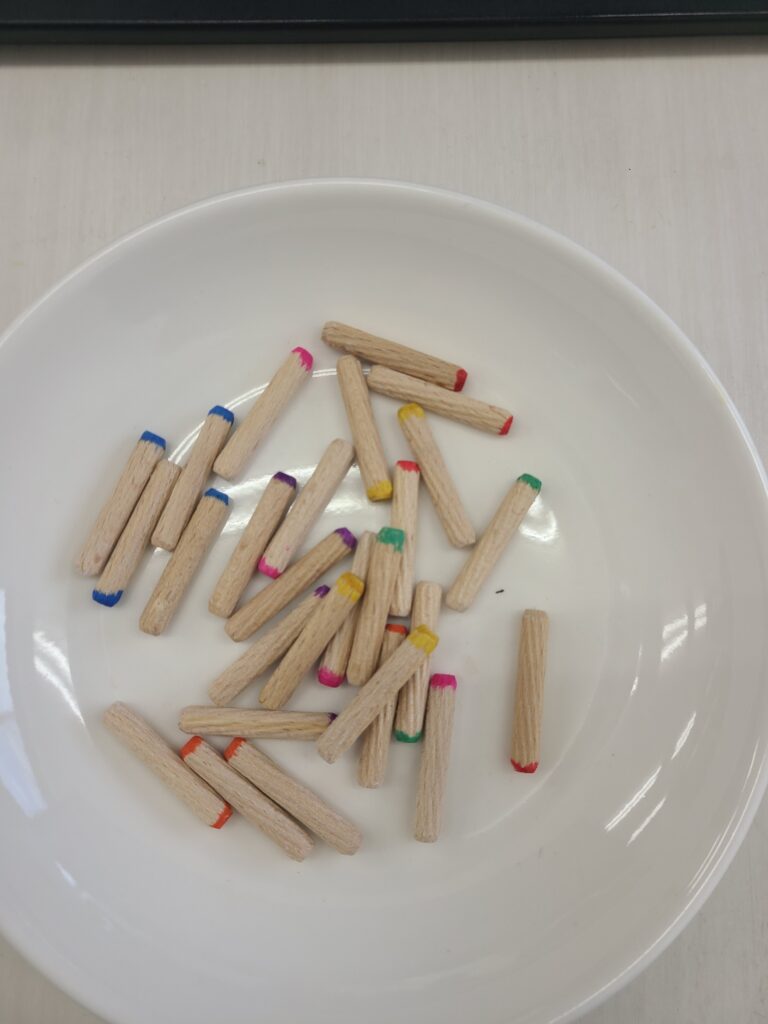
各車種膨大なオプションをもち、
プリウスだけで数万種類あるといわれます。
まさに巨大なオーダー生産工場です。
すさまじい種類があるので、
ともすれば、巨大な倉庫に大量にものを在庫ストックしてしまう生産方法になりかねません。
トヨタ生産方式の大野耐一さんの本に、
トヨタ生産方式は、カンバンによる後工程引取で、【自律神経】のように作り過ぎの無駄を省いている。
とあります。
まさにこれがトヨタ生産方式の強みの本質だと私は思います。
注文したものからカンバンが発行されるので、注文がなければカンバンが発行されません。
つまり注文以上のものを絶対に作らない仕組みなのです。
体にたとえると、暑くなったら、勝手に汗がでて体温を下げてくれます。
血糖値が上がったら勝手にインスリンがでて、血糖値を下げてくれます。そこに脳の介在はありません。
トヨタ7つの無駄のうち、最強のムダ、作り過ぎの無駄をなくすために、各工場が自律神経をもち働いているのです。
普通の会社だと、今月の生産量にもとづいて、計画し、適度に在庫しながら製品を作っておくと思います。
そのためおそらく他社がここまでオーダー生産をやろうとすると、管理システムと管理業務が肥大化してしまいますが、
カンバンというたった一つのアイテムですべてが自律神経化しているのです。
我々も、自律神経のような組織にしていく必要があると思いました。
以前、岐阜県でもトップオブトップの会社、福田刃物工業さんの社長さんと
ワンオンワンでお話するという機会がありました。
この話は深すぎるので、また後日お話したいと思います。
そこでは、ワンマンよりも、みなが自律的に働く会社の方が強い。
そうおっしゃられていました。
ちなみに、福田刃物工業の社長さんは、NEC半導体事業部出身の超絶エリートです。
そのどう考えても、私のATOM並のプロセッサと違い、
intelでいったら、corei9、AMDでいったら、RIZEN9並の処理能力なんですが、
それでも、皆が意見を出し合う環境を構築されています。
会社には自由な気質があふれ、皆がいきいきと働いていました。
私もガチガチに管理された生産工場というのは私はあまり好きではありません。
ものづくりの楽しさの本質とはずれるような気がするからです。
そのため、オフィスも含めた全員に原則をインストールする必要があるのです。
動作経済6原則
この実験は、動作経済6原則を用いてどのように動作を効率化していくか?
という講義内容です。
擬似的な作業を作ります。
ワークバケットに色分けされたダボを所定の穴にいれていく。
という簡単な作業内容になります。
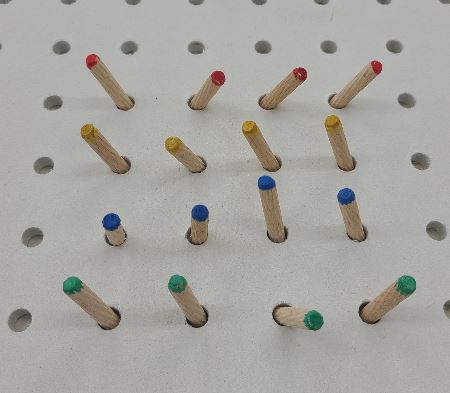
最初の一回は自分なりのやり方で施工していきます。
平均は45秒かかります。
つぎに、このワークバケットから、
いらないモノを撤去します。
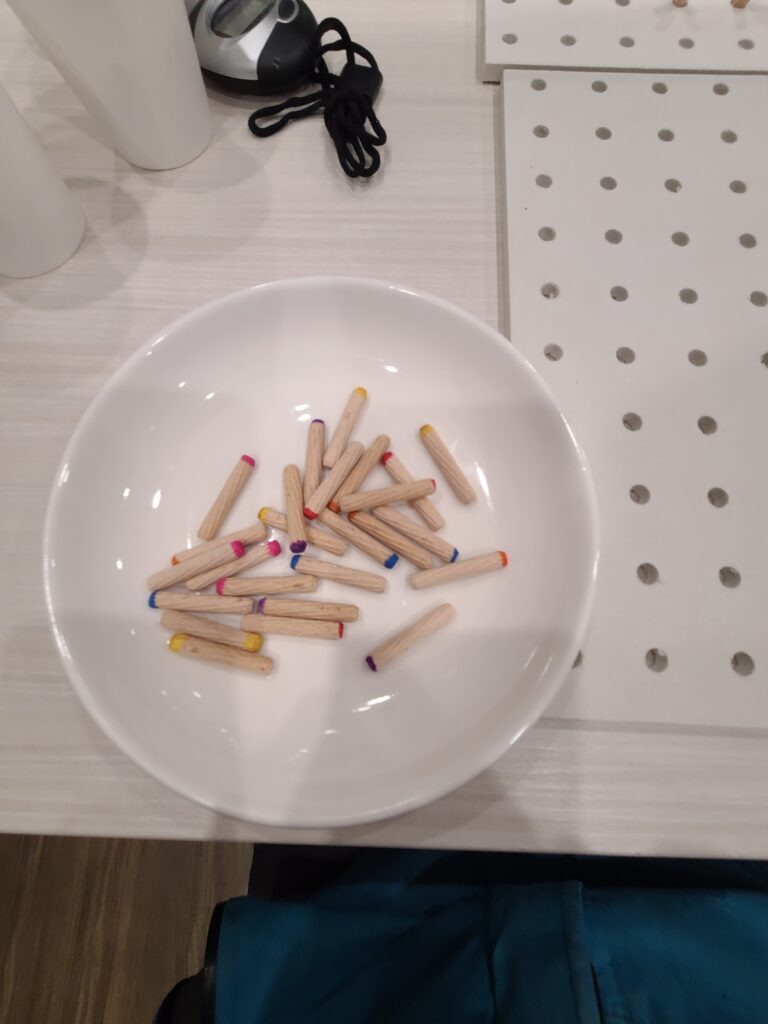
すると、ここから生産性が上がり始めていきます。
45秒→32秒に改善。
つまり探す動作がなくなるので、選択が早くなり、作業が効率化していきます。
これはトヨタの5Sでいうところの整理になります。
いらないモノの山が探すという無駄を発生させ、生産性を落としていることが実体験として経験できました。
次に整頓を行います。
使う順番に並べ替えていきます。
これが整頓
整頓することにより、細かい探す動作がなくなり高速化します。
ここで45秒→32秒→29秒へ
ここから、動作経済2の型、両手を使う。という改善に入ります。
両手改善では、両手を同時に動かし、2本づつセットしていきます。
ここでは2本を同時に入れるので、生産性が瀑上がりします。
45秒→32秒→29秒→19秒へ
ここから距離改善をします。
距離改善は、動作距離を極限まで短くする動作です。
こちらは、動作距離について、最短動線を描くような配置にします。
これによって、動作は最短距離でいくようになり、高速化していきます。
いやいや、距離なんて大したことないでしょ!
言われますが、この効果は地味に効いてきます。
なんと16秒へと改善されました。
45秒→32秒→29秒→19秒→16秒
原理原則だけを伝えて作業をしてもらったところ、なんと3分の1のスピードで生産することができるようになりました。
生産性3倍ということです。
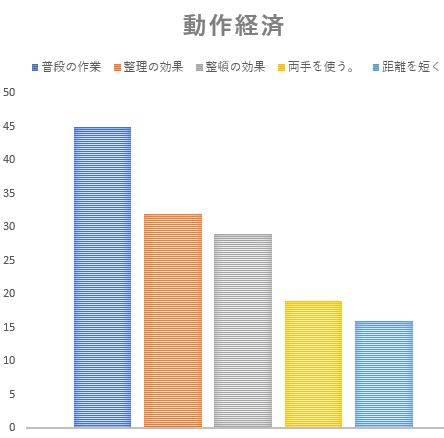
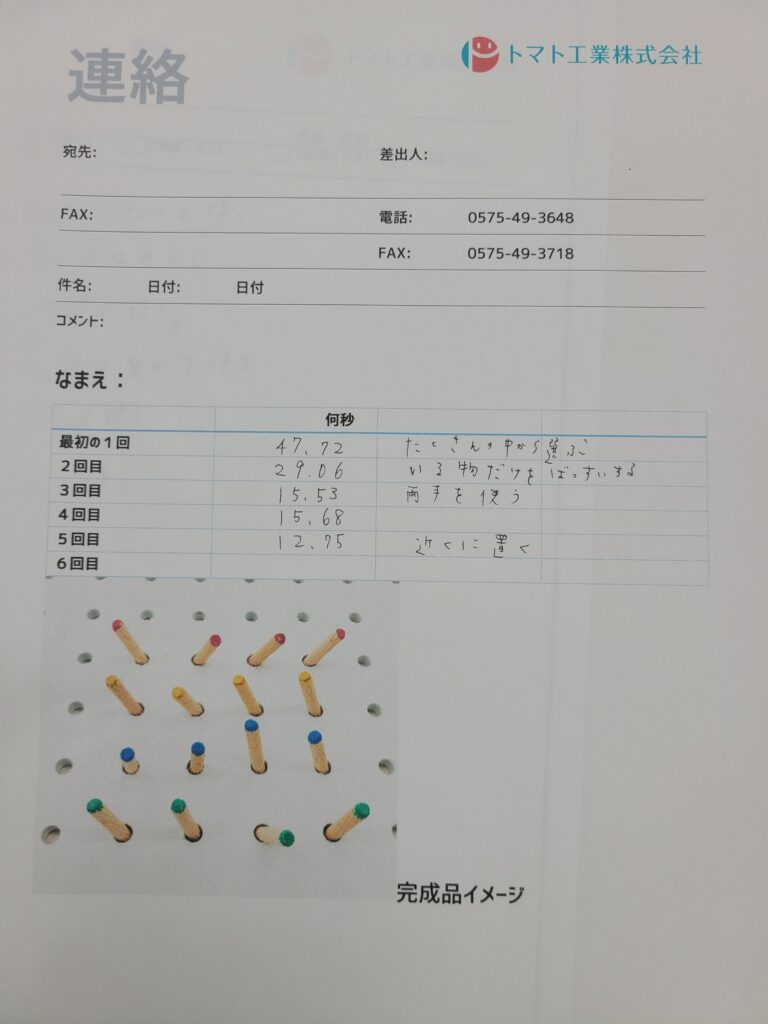
全員が大幅な生産性アップを果たしました。
そして、それは今後の生産活動をすこしづつ高速化していくものになるような気がします。
原理原則をきちんと理解し、どんなときでもいつでも使えるように日々の活動で活用していく必要がありますね❢❢
というわけで実験大成功しました。
以上馬渕からのレポートでした。