有孔ボード製作機械、有孔加工機での加工とは
パンチボード・有孔加工機での製作
有孔加工機械での加工を行っております。
ドリリングセンタ、DC684です。
第6世代の最新鋭機です。
他にも最新の設備で加工しております。
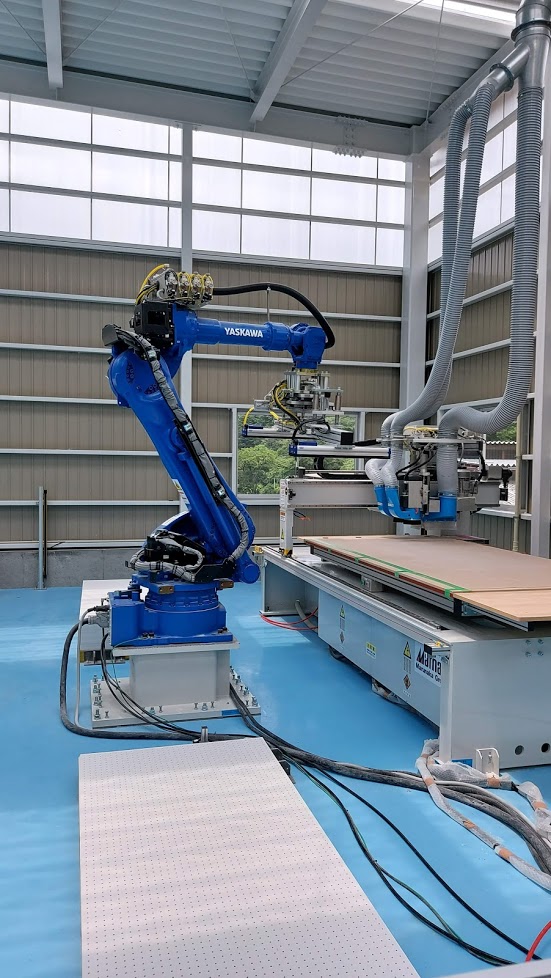
ボーリングヘッドはギア形式で最大10軸を動かしてドリルを開けることができます。
相当数の改善を施しすこしづつブラッシュアップしております。
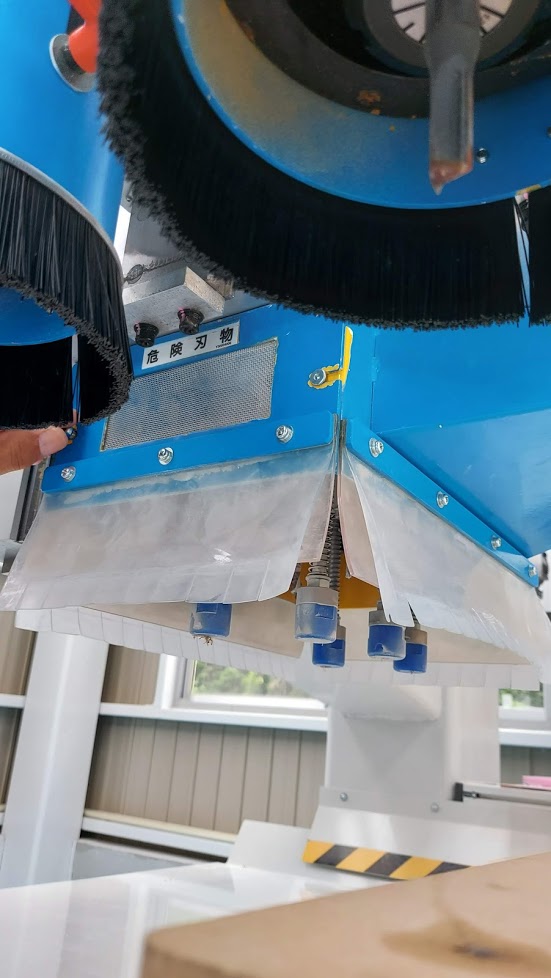
①切削・回転抵抗
固有のケイカル板などでは、内部の回転抵抗が高く、ドリルが途中で止まってしまうケースがありました。
10軸を同時に動かすので、切削抵抗がありましたが、刃物側の改善でなんとか対処しました。
②ドリル進入時のバリ
切削時にバリがでることがありましたが、これも刃物の改善により解消しました。
両側の罫引き刃の改善を施しています。
通常鉄工ドリルだと先端が尖っています。
これでも良いのですが、内部抵抗が高くなる傾向があり、彫りきれないまま加工がストップしてしまうケースがありました。
そのため改善でバリを少なくする特殊形状に変更をかけています。
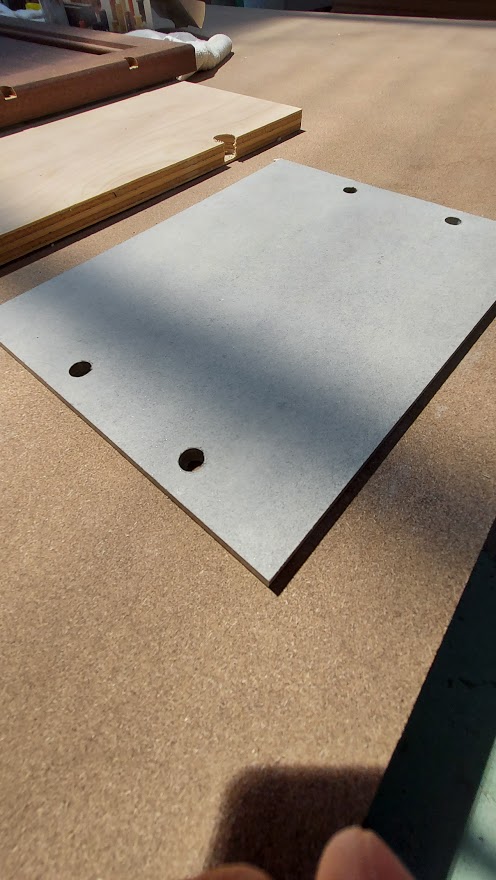
③ロボットハンドリング
有孔加工機にはYasukawaのロボットがついています。
これは完全無人加工を目指したものではあるのですが、問題があります。
通常エアーの力で最大40kgのボードを振り回します。
しかし有孔加工をするということはこのエアー吸着が逃げるということです。
加工後のハンドリングで吸着が外れてしまうケースがありました。
しかし穴をあけることでこの真空圧がきかず吸着から外れてしまうケースがあります。
これについては吸着パッドの改善にて対処しました。
④ピックアップ時の改善
ピックアップ摘み取り時に、ボードの真空圧で2枚、3枚と一緒に掴んでしまうケースがありました。
これについては、ピックアップ時のボード吸着形状を変更することで改善しました。
ロボットティーチングによって(ロボットに教え込ませる。)動作を最適化しています。
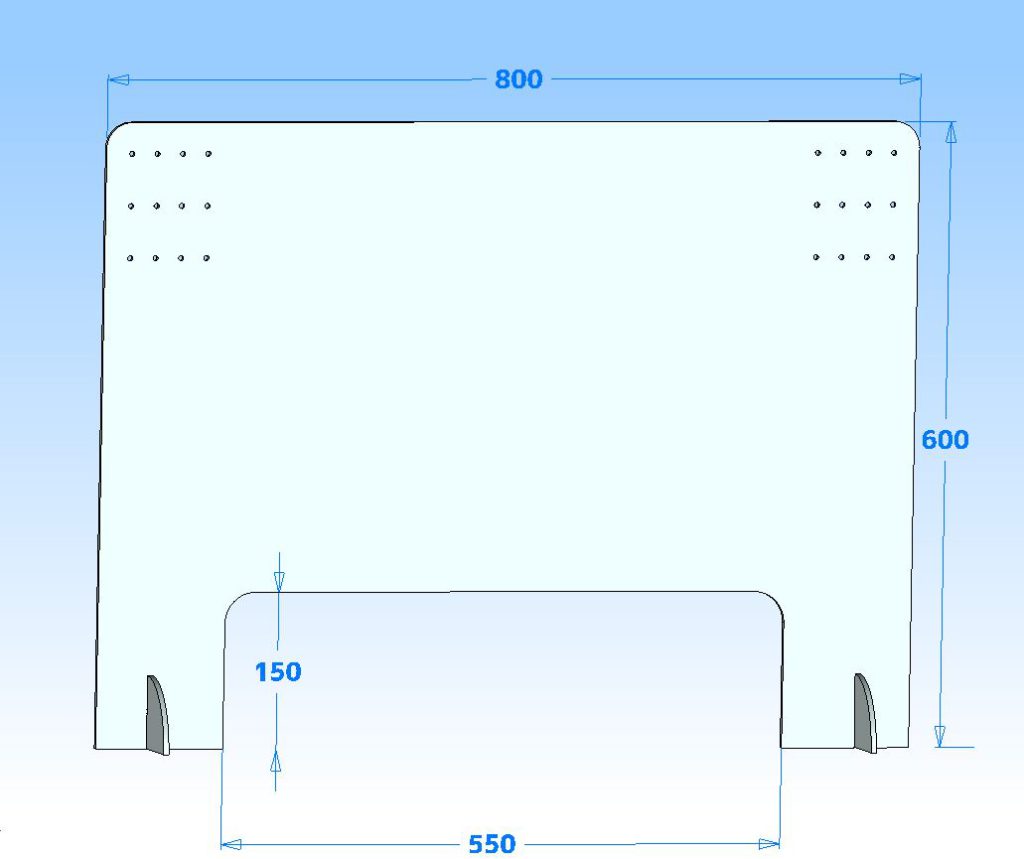
⑤刃物交換の改善
該当の機械は通常、60本等の大容量の刃物を搭載してドリルしていく加工が一般的です。
しかしながら非常に段取り替えが大変であり、ピッチ変更等も容易ではありません。
そのためトマト工業の有孔加工機では最大10本を交換すればよいので、交換にかかる手間が1/6で住むと言えます。
さらにこの10本の刃物については、ワンアクションで切削できるように改善をしているので、刃物交換が非常に楽になるというメリットがあります。
10分の1以下の労力で刃物交換ができるので小ロット多品種に対応することができます。
⑥抑え改善
板を自分で都度抑えて加工していきます。
しかしこの押さえが弱いと、板が浮き上がり、裏面にバリが出ることが確認されました。
そのためきちんと密着するように、適正な圧力に改善しています。
0.1mm単位でバネを改善しております。
⑦裏面バリ改善
裏面にバリがでますが、これも特殊な道具によってバリを軽減しています。
シャープボード有孔バージョン
このような機械でつくられたボードですが、
大人気のSHARPBOARDのシリーズにも展開され、有孔加工BOARDがラインナップされました。
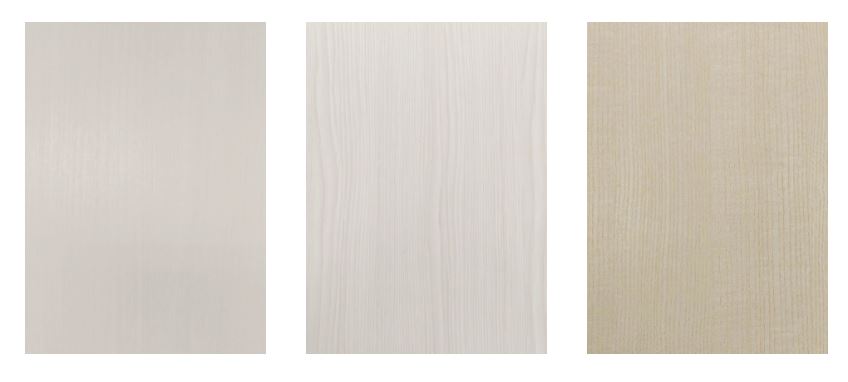
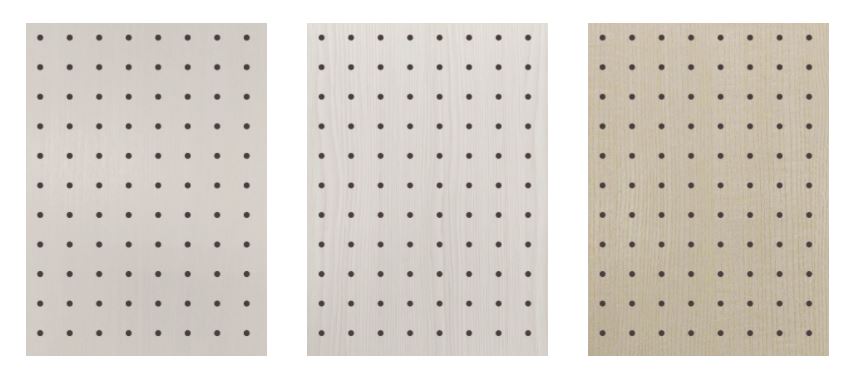
19種のラインナップがあります。
下記から販売しております。