工場のカイゼン例について
さてみなさまこんにちは
先日盆踊り大海があるってんで、子どもたちが言いまして
盆踊りやったことないなー。
なんて話をしてたんです。
そこで、私が
盆踊り教えてあげるわ。
毎年ロボット・ダンス言われてるやつ。
いいましたら
あんな踊りいいわ❢❢
言われましたよ。
一体どこへクレーム出したらいいんですかね。
どうもこんにちは
まぶちでございます。
今日は工場のカイゼン例についてお話したいと思います。
毎日平均3-4つものカイゼン例が出てきております。
我々田舎の中小企業なのでこの数、実は驚異的なんです。
みんなが考える。
ポイントは、各現場は自分たちで改善していく。
ということです。
パソコンには論理演算するCPUがあります。
各自がCPUになって行動していくことがこれからの高度化に必要不可欠である。
という考え方です。
パソコンのCPUも
単一コアのpentiumやceleronプロセッサからコアをいくつももつcoreiシリーズに変わっていきました。
時代の流れが単一コアから複数コアへ、複数コアからさらに複数スレッドに変わってきているように、
我々も多能工、マルチタスク、自分たちで考えるというように業態をかえていく必要があるのです。
そこで今回はうちの社員の素晴らしいカイゼンを皆様にお届けしようと思います。
ではスタート。
生産
生産とは工場であるところの核心にあたります。
核心。
北朝鮮でいうところの金正恩ですよね。
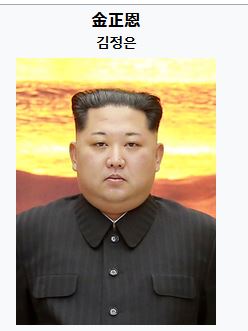
(どんなたとえだバカッ❢❢)
もっとも重要な部署になるため、日々のカイゼン活動が必須となります。
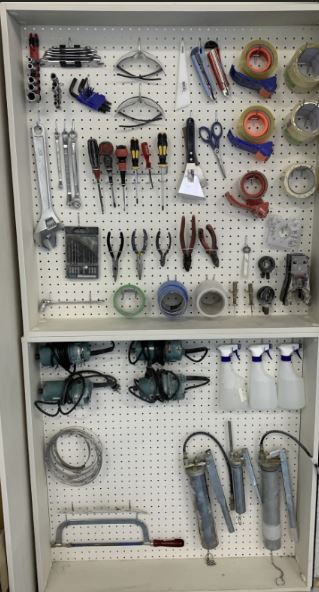
壁面収納がカイゼン活動の骨子です。
必要なもの以外を全部捨て、それ以外のものに注力する。
これが壁面収納の本質です。
前は各自が勝手に収納をどんどん作ってしまっていましたが、
収納量満杯になるまで収納が増えたので、以降収納制作は承認制となっております。
徹底的にモノを削減した上で収納を決めないと行けない。
それ以上入らないようにする必要がある。
という思想のもと収納を制作する必要があります。
従ってあるものを適当に入れるのではなく、
本当に必要なものだけを取りやすく収納することが重要になります。

わかりにくいのですが、再現写真がついておりまして、この写真を見れば戻す棚がすべてわかるようになっております。
下の段のオイルはカラーわけされており、直感的に識別できるようになっています。
当然初めての方でもわかりやすく、間違えないという仕組みです。
トマト工業の文化としてなにか問題がおこったとき
1.源流理論
と
2.仕組みカイゼン
というものがあります。源流理論については以前のブログにて記載があるので、今回は仕組みカイゼンについて解説します。
例えば、誰かがミスって不良品を出してしまった・・・あるいは機械に手を挟んでケガをしてしまったとします。
そのときよくあるのが、上長が
【なんでしっかりとやらないんだ!!】
と顔を真赤にして怒鳴りつけ、
【申し訳ありませんでした。
以後気をつけてしっかりやります!!】
と誤ったちょうど1週間後
しっかりと同じミスを繰り返す。
このようなことはないでしょうか。
我々の考え方はコレとは真逆の発想になります。
ケガをしたのであれば、個人の責任はほぼ問われません。
※標準作業以外のやり方をしていれば別ですが。
逆に上長や現場のリーダーに対し、
【なぜ、この問題が置きてしまったのか?】
を
ゼロ距離でリンダリンダくらい連呼する。
というやり方になります。
(うざっ❢)
例えば機械に手を挟んでしまったのであれば
【現場が気をつけなくてもできる仕組み】
がなかったのが問題であり、それ
を作ってあげればいいわけです。
生産の坂井を中心に毎日1個という驚異的なペースで改善が多く出ています。
彼の特徴は工場にある幅広い機械すべてに精通していることから、
工場の機械改善に特徴を持ちます。
最近は3Dプリンタを使った治具改善などもすすんでいます。
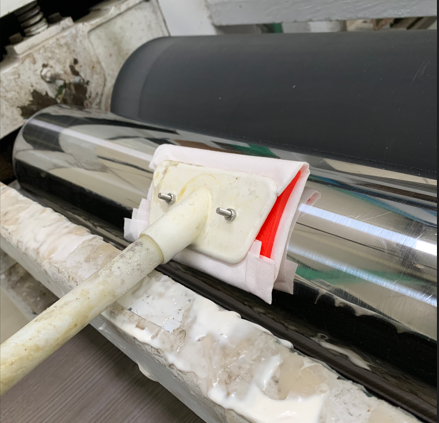
これが3次元治具、ロールコーター塗布道具になります。
婉曲した樹脂材をバーの先端に取り付けることで、手で洗うという行為自体がなくなります。
市販のフローリングワイパーと3Dプリンタ治具の合作となり、
以降手を近づけることが絶対になくなりました。
ここにおいては作業者は気をつけることすら必要なくなります。
これが【仕組み化】になります。
気をつけなくても手を挟まないということになります。
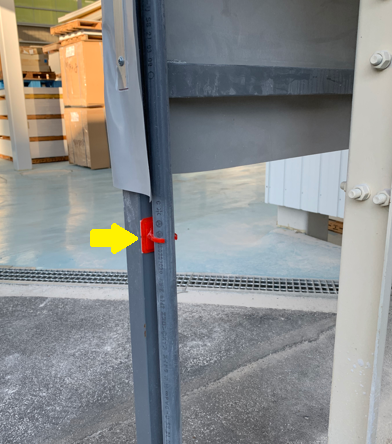
同じように、使う道具をさがしまわるのであれば専用のアタッチメントをつけて、最短動線上に置くことによって
だれでもいつでも最短で取り出せる仕組みができます。
【棒はそこにあるって何度行ったらわかるんだ❢❢怒❢】
ということが一切なくなります。
オペレーションカイゼン
よくあるのが、現場の工場に対しては作業改善を求めるものの、事務所がグッチャグチャという例があります。
私は工場でみんなと汗を流して立ち上げた工場なので、そうした考え方は最も忌み嫌います。
カマ●ドウマくらい大嫌いなのです。
(どんなたとえだ❢❢)
率先垂範しないと行けない立場なのにと思うわけです。
事務所が改善しない。
これは
税務署が脱税したり、
警察が盗みを働くと同義なのです。
オペレーションの改善こそ、工場改革の鍵となる。
コレは間違いないでしょう。
こちらはオペレーションの中嶋を中心に改善がでています。
彼の特徴はマニュアル化に特徴があり、毎日困ったこと、つまづいたことをわかるまで突き止め、
それをマニュアルに落とし込んでいます。
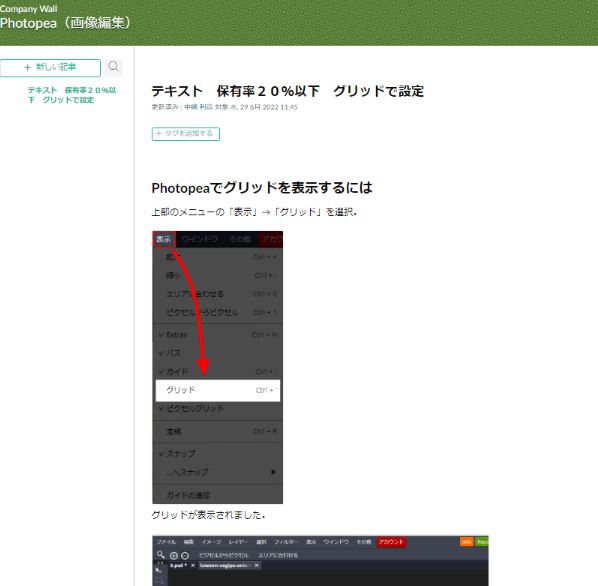
マニュアルというのは、とても大事で新しい人を即戦力にするためのツールです。
また教える側も教えるという手間が一切必要なくなります。
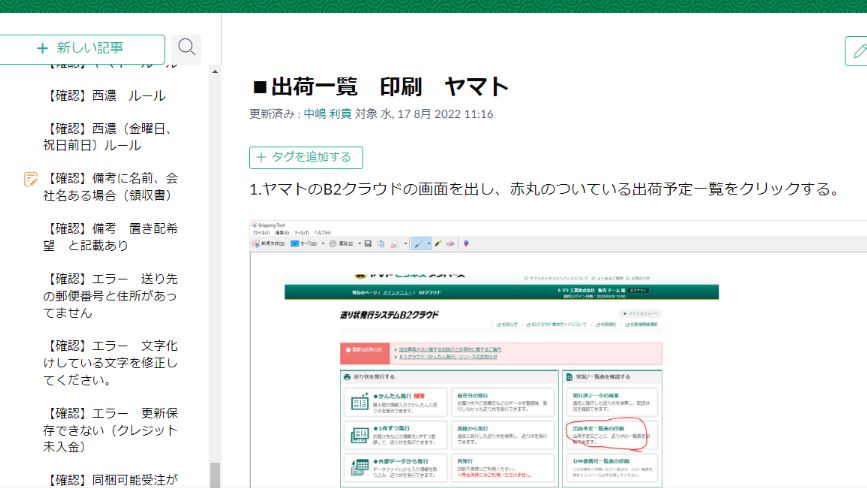
今会社には約1,000を超えるマニュアルがあり、クラウド上でみれるようになっております。
会社としてマニュアルを最重要視しているのは、私自身の経験によるものです。
私はパソコンでいうとCPUが遅く、メモリが少なく、一番の問題は、ハードディスクがぶっ壊れているということです。
覚えられずすぐ忘れる。
パソコンなら即ハードオフ行き
なんですが、長期記憶できないので、マニュアルにしておくことで、覚える必要がなくなります。
PCでいうところの
外付けハードディスクとして機能させることができます。
昔はしょっちゅう【社長?これはなんでしょうか?】聞かれてましたが、聞かれるたびにマニュアル化すること、
みんながマニュアルをつくることでこうした質問がなくなっていきました。
セールス改善
一方でセールスの改善も重要です。
たとえば、すし屋であれば、おやっさん、今日トロいくら?ときけば即答されるか、そもそも表示されています。
しかし製造業ではトロの価格を聞いたときに、平気で1週間とか立つのがざらなのです。
そこで、
90%以上の依頼を20分以内に解答する。
という戦術目標を立てて改善を繰り返しております。
せっかく問い合わせしていただいたお客様を
一切おまたせしない仕組みづくり
が重要になる、会社内でもっとも重要な改善になります。
営業の加藤を中心に改善を繰り返しております。
特徴はエクセル(現在は禁止:スプレッドシートに移行)
技術を活かして管理表を作ったり、独自の仕組みを開発しています。
現在はITEXPERTさんと協力して、オンラインで資材が発注出来る仕組みアプリを開発しました。
改善提案大賞候補になります。
この仕組は、オンライン上で接着剤やボードの数を入力すれば、勝手にメールがお客さんに行くというものです。
従来は現場の要望を受けて事務所でFAX等をしておりましたが、その必要がなくなりました。
これによって現場のタブレットからなくなった時点で発注ができるようになりました。
資材発注漏れによる納期の不安定化を解消したこと
煩雑な資材発注業務から開放されたこと
専門により詳しく解説をしたいと思います。
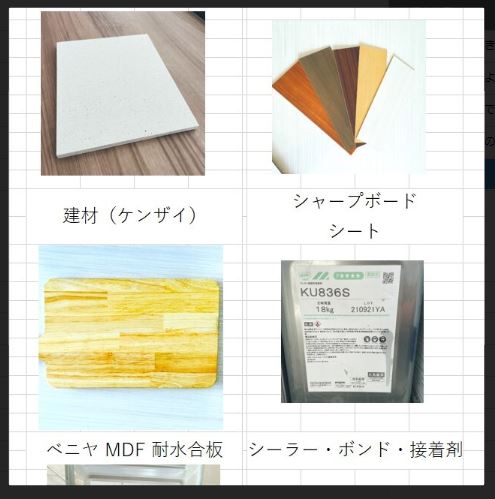
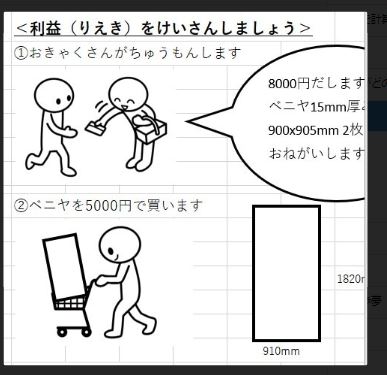
工場の実習生むけマニュアルです。
このように我々一人一人が、自分たちで考えながら業務を改善しています。
ただたんに作業するだけではなく、自分たちの職場は自分たちで改善するんだ❢❢
という意識がとても嬉しいとともに、感謝の毎日です。
みんなありがとう❢❢
工場の改革はやりたいことだらけなのですが、すこしづつできることが増えて嬉しく思いますね。
ではまたーーー❢❢